FLEXGEAR
FVA 708 II | IGF-Nr. 19844-N
Einfluss des Werkzeugverschleißes auf die Bauteilrandzone und die Bauteillebensdauer beim 5-Achs-Fräsen von Großverzahnungen
Die Ergebnisse des vorangegangenen Forschungsvorhabens IGF 17890 sowie frühere Untersuchungen zum Hartfräsen mit Schaftfräsern legen nahe, dass bei der Hartfeinbearbeitung von Großverzahnungen mittels 5-Achs-Fräsen signifikanter Werkzeugverschleiß entsteht. Der Stand der Technik zeigt darüber hinaus, dass sich der Werkzeugverschleiß unmittelbar auf die Eigenschaften der Bauteilrandzone auswirkt. Diese ist entscheidend für die Tragfähigkeit von Verzahnungen. Im Projekt wurde der Einfluss des Werkzeugverschleißes auf die Bauteilrandzone und die Bauteillebensdauer beim 5-Achs-Fräsen von Großverzahnungen untersucht.
Bislang war nicht bekannt, ab welcher Randzonenbeeinflussung durch das 5-Achs-Fräsen die Tragfähigkeit der Verzahnung signifikant herabgesetzt wird. Aus der Untersuchung von Werkzeugen, bei deren Verwendung eine Beeinträchtigung der Randzone detektiert wurde, kann ein Werkzeugverschleißkriterium abgeleitet werden, das den Standweg anwendungsbezogen und funktionsgerecht begrenzt. In diesem Zusammenhang erfolgte die Festlegung einer geeigneten Messgröße für den Werkzeugverschleiß beim 5-Achs-Fräsen von Verzahnungen. Zur Erhöhung der Prozessstabilität wurde überprüft, ob der Werkzeugverschleiß durch den Einsatz von Sensorik im Prozess zuverlässig erkannt wird. Im Rahmen der Werkzeuguntersuchung wurde zudem untersucht, wie sich der Verschleiß des Fräswerkzeugs ausbildet und ab welchem zerspanten Volumen bzw. Schnittweg das abgeleitete Verschleißkriterium erreicht ist.
Insbesondere bei Großverzahnungen war auf Grundlage der Erkenntnisse aus dem vorangegangenen Forschungsvorhaben IGF 17890 davon auszugehen, dass der Werkzeugstandweg nicht für die Fertigung eines kompletten Bauteiles ausreicht. Daher war zu untersuchen, ob und mit welcher Strategie ein Werkzeugwechsel bei gegebenen Qualitätsanforderungen umgesetzt werden kann. Deshalb musste in diesem Forschungsvorhaben der Zusammenhang zwischen zerspantem Volumen, Werkzeugverschleiß, Bauteilintegrität und Tragfähigkeit ermittelt werden. Das Ziel war es, die Beeinflussung der Bauteilintegrität und somit der Tragfähigkeit durch die Veränderung des Werkzeugzustandes für wirtschaftlich relevante Bauteilgrößen vorhersagbar zu machen.
Die fünf anfangs gestellten Forschungsfragen konnten wie folgt beantwortet werden: Zur Charakterisierung des kritischen Werkzeugverschleißzustands ist das Auftreten von Ausbrüchen als Abbruchkriterium zu definieren. In den Versuchen konnte bis zu einer Verschleißmarkenbreite von VB = 40 μm prozesssicher und maßhaltig gefertigt werden. Hinsichtlich der Werkzeugstandzeit, welche noch eine akzeptable Randzonenintegrität zur Folge hat, wurde erarbeitet, dass mit entsprechender Werkzeuggeometrie, Substrat, Bearbeitungsparametern und Beschichtung Vorschubwege von mehr als einem Kilometer möglich sind. Die generelle Machbarkeit der Prozessüberwachung des Werkzeugverschleißes im 5-Achs-Fräsprozess wurde mittels piezoelektrischer Kraftmessung nachgewiesen. Die Fragestellung, ob sich maschinenintegrierte Sensorik wie bspw. dehnmessstreifenbasierte oder spindelstrombasierte Systeme zur Verschleißüberwachung eignen, bedarf weiterer Forschung. Da in den Untersuchungen sehr lange Standwege erreicht wurden, wurde eine maschinenintegrierte Sensorik in diesem Projekt nicht betrachtet. Ein Wechsel des Werkzeugs während der Bearbeitung eines Bauteils hat negative Auswirkungen auf die geometrische Qualität. Selbst wenn das Werkzeug mit hochgenauen Werkzeugeinstellgeräten eingestellt und die Geometrie des Werkzeugs genau vermessen wurde, kommt es zu einem Versatz in der Verzahnung. Hinsichtlich der fünften Forschungsfrage, welches Qualitätsmerkmal der Verzahnung am sensibelsten auf Werkzeugverschleiß reagiert, kommt es auf die eingesetzte Frässtrategie an. Aus den Untersuchungen innerhalb dieses Forschungsvorhabens ergaben sich folgende Erkenntnisse, die in zukünftigen Untersuchungen weiter vertieft werden müssen: Wenn die Lücken nacheinander fertig gefräst werden, reagieren zuerst die Zahndicke und der Teilungsfehler auf fortschreitenden Verschleiß. Wenn in Ebenen gefräst wird, also sukzessive reihum jeweils eine Ebene vom Kopf bis zum Fuß der Verzahnung bearbeitet wird, reagieren zuerst die Profilform und der Profilwinkelfehler.
Im Rahmen des letzten Arbeitspunktes wurde die Anwendung der unter Laborbedingungen ermittelten Forschungsergebnisse in einem industriellen Umfeld geprüft. Es wurde ein schrägverzahntes Stirnrad mit einem Durchmesser von d = 680 mm und einem Modul von mn = 18,3 mm gefertigt. Für die Schlichtbearbeitung wurde für das gesamte Zahnrad ein Schaftfräswerkzeug benötigt. Nach der Bearbeitung wies dieser Schaftfräser eine Verschleißmarkenbreite von VB = 38 μm auf, die von der prognostizierten Verschleißmarkenbreite aus vorherigen Arbeitspaketen von VB = 40 μm nur aufgrund von Messungenauigkeiten durch das optische Messverfahren abwich. Die Vermessung des Zahnrades ergab eine Toleranz der Teilungs-Einzel- und Summenabweichung von IT3. Die mittels taktilen Messverfahren ermittelten Oberflächenrauheitsmessungen ergaben eine maximale Oberflächenrauheit von Ra < 0,7 μm und ein Rz < 4,5 μm.
Bei der Messung der Eigenspannungen mit dem Verfahren der Röntgendiffraktometrie und dem Elektropolieren wurden Druckspannungen in der Randzone identifiziert. Die Messung ergab eine Beeinflussung bis zu einer Tiefe von t = 30 μm. Geringere Druckspannungen wurden bei erhöhter Schnittgeschwindigkeit und hohem Zahnvorschub aufgrund der hohen thermischen Energie gemessen. Eine Untersuchung der Gefügestruktur mittels Gefügeschliffe ergab keine Auffälligkeiten. Insgesamt wurden durch die Ergebnisse aus der Fertigung im industriellen Umfeld die Ergebnisse der vorhergehenden Labor- und Analogieversuche bestätigt.
Die im Vorhaben entwickelte Technologie ist durch den empirischen Charakter des Vorhabens für den untersuchten Parameterraum gültig. In zukünftigen Vorhaben sollten deshalb numerische Ansätze verfolgt werden, um diesen Gültigkeitsbereich zu erweitern. Ferner sollte, wie erwähnt, die Prozessüberwachung weiter am Beispiel 5-Achs-gefräster Verzahnungen erforscht werden. Die sehr geringen Zerspankräfte erschweren die messtechnische Erfassung und somit die Prozessüberwachung bzw. Prozessregelung. Vorteile einer Prozessüberwachung mittels maschinenintegrierter Sensoren sind im Gegensatz zu externen Sensoren die Anwendbarkeit im industriellen Umfeld ohne zusätzliche Aufwände - auch für KMU. Die erarbeiteten Grundlagen zur messtechnischen Charakterisierung der Oberflächentopographie und die Korrelation mit der zu erwartenden Lebensdauer sind ausreichend für die Validierung an der untersuchten Werkstoff-, Schneidstoff- und Parameterkombination. Fundamentale Kenntnisse, die generell angewendet werden können, könnten durch die numerische Modellierung der Randzone und die Veränderungen durch den Zerspanprozess entwickelt werden.
Das IGF-Vorhaben IGF-Nr. 19844-N der Forschungsvereinigung Antriebstechnik e.V. (FVA) wurde über die AiF im Rahmen des Programms zur Förderung der Industriellen Gemeinschaftsforschung (IGF) vom Bundesministerium für Wirtschaft und Energie aufgrund eines Beschlusses des Deutschen Bundestages gefördert.
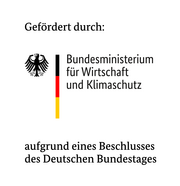