Quasi.BAT 2
FVA 630 II, IGF-Nr. 16 N
Qualitätssicherung in der Produktion von Lithium-Ionen-Batterien für Elektromobilitätsanwendungen
Die Kosten des elektrischen Hochvoltspeichersystems machen auch zukünftig mit ca. 300 €/kWh [1] den größten Anteil der Kosten elektrifizierter Antriebsstränge aus und sind wesentlicher Hemmschuh bei der Marktdurchdringung von E-Fahrzeugen. Um die Qualität von Lithium-Ionen-Batterien zu verbessern und schon im Produktionsprozess eine Voraussage über die späteren Leistungseigenschaften der Batterie treffen zu können, wurden im Rahmen des Projekts Quasi.Bat II - Qualitätssicherung in der Produktion von Lithium-Ionen-Batterien für Elektromobilitätsanwendungen – die Sensitivitäten der qualitätsbeeinflussenden Prozesskenngrößen und qualitätsrelevanten Produkteigenschaften erforscht. Die Ergebnisse schaffen ein grundlegendes Verständnis von den qualitätsbeeinflussenden Parametern im Produktionsprozess von Lithium-Ionen-Batterien und ermöglichen, Kostenpotenziale zu generieren, indem Produktionsprozesse gemäß tatsächlichen Qualitätsanforderungen ausgelegt werden.
Ziel der ersten Projektphase, des am Werkzeugmaschinenlabor und dem Lehrstuhl Production Engineering of E-Mobility Components der RWTH Aachen bearbeiteten Projekts, war die Identifikation und Analyse der qualitätskritischen Produktionsschritte in der Batterieproduktion. In der zweiten Projektphase im Projekt wurde die großserientaugliche Ausgestaltung von Qualitätsregelkreisen für ausgewählte Produktionsschritte und Testverfahren im Produktionsprozess der Batteriezelle zur kontinuierlichen Bestimmung der Batteriequalität entwickelt. Dabei wurden im Verlauf der zweiten Projektphase, aufbauend auf den Ergebnissen der ersten Phase, erfolgreich die Prozessstörgrößen im Produktionsprozess identifiziert und nach den Auswirkungen auf die Leistung der Batterie priorisiert. Auf Basis einer Analyse der Auswirkungen der Störgrößen auf den gesamten Produktionsprozess ließen sich Aussagen zu einer optimalen Konfiguration von Fertigungsschritten treffen. Für die in der ersten Projektphase ermittelten Prozessschritte konnten auf Basis dieser Ergebnisse Qualitätsregelkreise abgeleitet werden. Die Validierung der Regelkreise auf Großserientauglichkeit bildete den Abschluss des Projekts.
Die in diesem Projekt genutzte Anlagentechnik ist Teil des Elektromobilitätslabors (eLab) der RWTH Aachen, dessen Infrastruktur Forschungsprojekten und Industriepartnern zur Verfügung gestellt wird. Neben der Infrastruktur für die Fertigung und Beforschung der Komponenten des elektrischen Antriebsstrangs gehören die Bereitstellung von Prüftechnologien sowie Büro- und Werkstattflächen zum Leistungsspektrum am eLab, das auf 800 m² Hallenfläche abgebildet ist.
Download: Kurzbeschreibung
Weitere Informationen zum Projekt für Mitglieder in THEMIS.
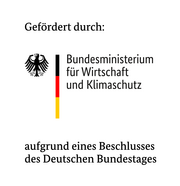